Vacuum infusion
Vacuum infusion (also called Resin Infusion) is an industry wide term describing a composite manufacturing process whereby the fabric reinforcement and resin are prepared separately.

Resin infusion is used in open moulded composite manufacture and involves the tailoring, positioning and laying up of all the reinforcement fabric in a dry state, followed by the application of the vacuum bag. Before the mould is fully sealed, various inlet taps are positioned and linked into a network for introducing the liquid resin. The physics behind the process means that because of a pressure differential the resin is “sucked” up the inlet tubes and dispersed across the dry fabrics, sometimes aided by channels or grooves in the core material, or mesh that is designed to aid uniform fluid flow.
The number of companies using Resin Infusion is steadily growing. The technology has several benefits:
⇒ high and repeatable quality
⇒ reduced resin content
⇒ high fiber/volume fraction (weight reduction)
⇒ mechanical properties of the final product are significantly higher
⇒ less labour time
⇒ less time in the mould
⇒ very clean process
⇒ almost zero emission (closed mould)
Switching to infusion does not always mean that the producer will have to make big changes to the laminate specification. However some fibres do not allow traditional resins to flow particularly well, hence infusion resins are modified to allow greater flow rates than would otherwise be possible. We can help with specification alterations and provide guidance as to which fibres and resin systems are best suited. Most of our clients specify or change to the infusion process as a step towards improved structural properties and weight reductions over the hand laminated cost option.

Switching to infusion does not always mean that the producer will have to make big changes to the laminate specification. However some fibres do not allow traditional resins to flow particularly well, hence infusion resins are modified to allow greater flow rates than would otherwise be possible. We can help with specification alterations and provide guidance as to which fibres and resin systems are best suited. Most of our clients specify or change to the infusion process as a step towards improved structural properties and weight reductions over the hand laminated cost option.

Technology benefits
- high and repeatable quality
- less labour time
- reduced resin content
- very clean process
- high fiber/volume fraction (weight reduction)
- almost zero emission (closed mould)
- higher mechanical properties of the final product
More questions regards to our products & services?
Then feel free send us a e-mail or give us a call and we’ll go from there!
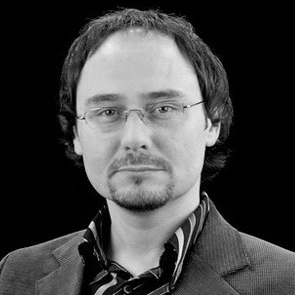